CNC Machining: From Concept to Finished Product
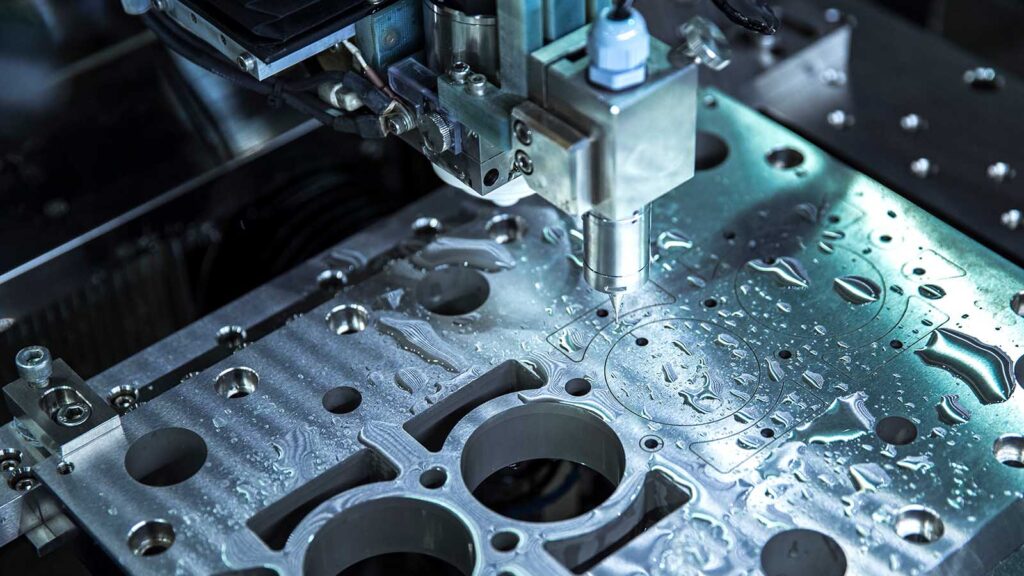
Introduction
In today’s fast-paced manufacturing landscape, precision and efficiency are paramount. Computer Numerical Control (CNC) machining has revolutionized the way we create parts, offering unparalleled accuracy and repeatability. This article delves into the intricate process of CNC machining, exploring how it transforms initial concepts into tangible, high-quality products.
Understanding CNC Machining
CNC machining is a subtractive manufacturing process that utilizes computer-programmed controls to manipulate machine tools. Unlike traditional machining, which relies on manual operation, CNC machining automates the process, minimizing human error and maximizing precision.
The CNC Machining Process
The journey from concept to finished product involves several key stages:
-
CAD/CAM Design:
- The process begins with Computer-Aided Design (CAD), where engineers create detailed 3D models of the desired part.
- These models are then imported into Computer-Aided Manufacturing (CAM) software, which generates the toolpaths and G-code necessary to control the CNC machine.
-
Material Selection:
- CNC machining can work with a wide range of materials, including metals, plastics, and composites.
- The choice of material depends on the specific requirements of the product, such as strength, durability, and cost.
-
Machine Setup:
- The selected material is securely mounted onto the CNC machine.
- Cutting tools are carefully chosen and installed, and the machine’s control system is loaded with the generated G-code.
-
Machining Operation:
- The CNC machine executes the programmed instructions, precisely moving the cutting tools to remove material from the workpiece.
- This process may involve various machining operations, such as milling, turning, drilling, and grinding.
-
Quality Control:
- Throughout the machining process, rigorous quality control measures are implemented to ensure accuracy and consistency.
- This may involve using precision measuring tools and techniques to verify dimensions and tolerances.
-
Finishing:
- Once the machining is complete, the finished product may undergo additional finishing processes, such as deburring, polishing, or coating, to enhance its appearance and performance
Types of CNC Machines
Several types of CNC machines are commonly used, each designed for specific applications:
- CNC Milling Machines: These machines use rotating cutting tools to remove material from the workpiece.
- CNC Lathes: These machines rotate the workpiece while a cutting tool removes material.
- CNC Routers: These machines are used for cutting and shaping various materials, including wood, plastics, and composites.
Advantages of CNC Machining
CNC machining offers numerous advantages over traditional machining methods:
- High Precision and Accuracy: CNC machines can achieve extremely tight tolerances, ensuring consistent and accurate results.
- Increased Efficiency and Productivity: Automated operation allows for faster production times and reduced labor costs.
- Complex Geometries: CNC machines can create intricate and complex shapes that would be difficult or impossible to produce manually.
- Repeatability: CNC machining ensures that every part is produced to the same specifications, minimizing variations.
Applications of CNC Machining
CNC machining is used in a wide range of industries, including:
- Aerospace: Manufacturing of aircraft components.
- Automotive: Production of engine parts and other vehicle components.
- Medical: Creation of surgical instruments and medical devices.
- Electronics: Fabrication of electronic components and enclosures.
Conclusion
CNC machining has transformed the manufacturing industry, enabling the production of high-quality, precise parts with increased efficiency. As technology continues to advance, CNC machining will play an even greater role in shaping the future of manufacturing.